Sept. 16, 2010
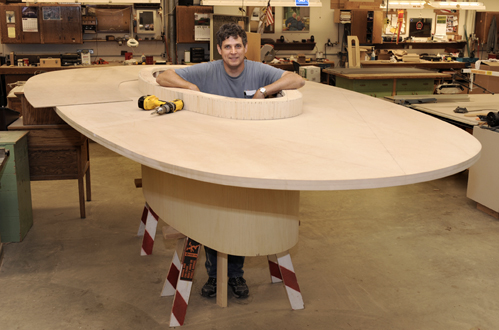
Carpenter Randy Fiscus stands in the center of the table frame, which rests on sawhorses. Fiscus worked on the project on and off from late January through this week. Photos by Bob Elbert.
Conference table in new research building was a team effort
by Anne Krapfl
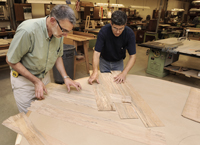
Mark Chidister (left) and Randy Fiscus begin the task of laying out the veneer strips.
It'd be simple to tag this project a labor of love. You might need to compare it, however, to the love of first-time parents coddling their inconsolable newborn in the middle of the night. There have been a few "What should we try now?"s along the way -- but always a solution, too.
A one-of-a-kind-in-the-world table will grace the first floor conference room in the new Biorenewables Research Laboratory (BRL) being dedicated on Friday. Student-designed and employee-created, in part with wood salvaged from campus trees, the table is sure to be a conversation starter in a building that's all about sustainability.
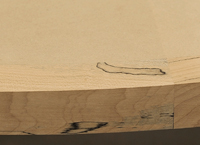
The color caused by fungi in spalted wood is desired among wood artists.
For the record, it's a big table: 15 feet by 7.5 feet at the widest points of its oval shape and weighing about 850 pounds. It was built in seven pieces and fitted together on site. It seats 14-16 people, who have access to electrical outlets, computer ethernet and a control panel for cameras and LCD panels in the room from a center, stacked oval.
"Hopefully, people appreciate the unique qualities of this table," said Mark Chidister, associate professor of art and design and one of several key players who worked on the table. "Each step along the way found us puzzling through how to make it work."
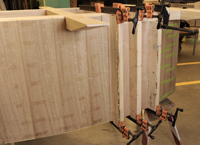
Wood vices helped Randy Fiscus apply burr oak veneer strips to the table base.
The design
A senior-level integrated studio arts class Chidister taught last fall took on the design as a class assignment. When BRL project manager Jon Harvey inquired about a collaborative project for the conference room, Chidister said initially he was reluctant because a table that large couldn't be built in the College of Design's wood shop. Eventually he landed on the idea of a student competition and Harvey approached Randy Fiscus in facilities planning and management's carpenter shop about building the winning design. So, early in the semester, about 10 student designs were presented to a committee from the new building, and senior Brian Dreesman's proposal was selected.
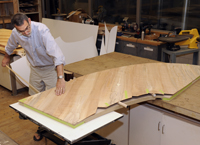
Mark Chidister used a series of dowels to center the maple veneer layer on the tabletop section during gluing.
Dreesman graduated from Iowa State in May and was one of 24 emerging young artists to exhibit at the Des Moines Arts Festival in June. Later this month, he and three colleagues will open Carbon 6 Studio, specializing in wood furniture and metals work, on Kellogg Avenue in Ames.
The construction
In January, Fiscus received Dreesman's design drawings and went to work. Due to the size of the table and the expansion potential of the wood, thin (about 1/16 inch) veneer strips would be applied to a stable plywood substrate. From the wood inventory in the ISU TreeCYcle program, Dreesman selected burr oak for the table base and center oval, and spalted maple for the table surface. Spalting is color in wood created by fungi, typically in distressed or even dying trees. The unique colors and patterns it creates add depth and beauty to items created from spalted wood.
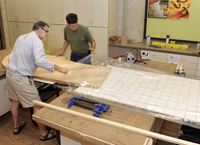
Mark Chidister (left) and Randy Fiscus slide a tabletop quadrant into the vacuum bag before boosting the pressure inside it during gluing.
Dreesman's wood selections were delivered to a Marshalltown kiln for drying. The anticipated month-long process stretched into two-plus, and it was early July before the wood was back on campus and Dreesman and Chidister could cut it into veneer strips at the College of Design. Fiscus, the patient carpenter, had completed the plywood table frame and was waiting to resume work on the project.
The humidity!
With practically no maple veneer to spare, Chidister and Fiscus painstakingly laid out the veneer strips to more vividly display the whites and grays of the spalting. Viewed from above, the array forms an open-winged butterfly. Fiscus trimmed the excess edges and glued the strips edge to edge, creating four sheets.
However, he noticed the summer humidity in his nonclimate-controlled shop was causing visible changes to the lengths and widths of the veneer strips. So, in early August, the tabletop, now in quadrants, was moved back across campus to the College of Design's small -- but climate-controlled -- wood shop. To maximize the adhesion of veneer strips to the wood base and thus the flatness of the tabletop, each quadrant was placed in a vacuum pressurized bag for about two hours of drying.
Humidity was an issue -- but less so -- for the burr oak veneer going on the table base and center oval, and Fiscus was able to complete that task in his shop.
Shining it up
Last week, painter Mark Mather waded into the task of sealing the wood. There is no stain in the table, just a couple of environmentally friendly tung oil products that he sprayed, brushed or hand-rubbed in. At last count, Mather had applied eight coats to the tabletop sections -- and he wasn't done yet.
Fiscus is scheduled to spend a good chunk of Sept. 16 in the BRL conference room, assembling the table pieces for the final fitting. Electrician Jeff Lamb and information technology services' Matt Darbyshire will work together to run electricity to the table's center oval and install LED light strips and the media package purchased for the conference room.
After the last four or five months, Fiscus readily admits he's become a little possessive of the big oval. The projects that test you the most often turn into favorites, he said.
Did he fine-tune some of his woodworking skills? Yes.
Was it stressful work at times? Yes.
Would he accept another one-of-a-kind-in-the-world project? Absolutely.
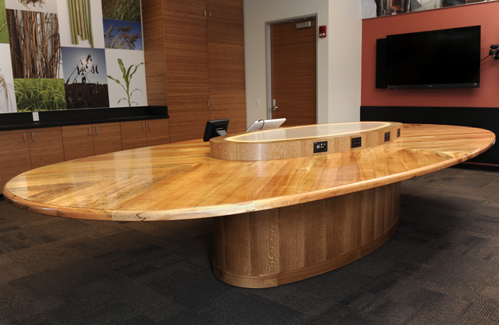
The completed table in the first-floor conference room of the Biorenewables Research Laboratory.