 |
|
|
June 13, 2003
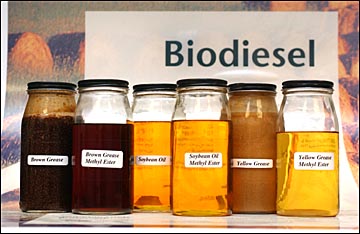 |
Biodiesel can be made from soybean oil (middle two jars), but it also can be
made from from brown grease (left two jars) or yellow grease (right two
jars). Brown grease can come from a rendering plant or a sewer trap. Yellow
grease also can come from a rendering plant or from restaurants. Photo by
Bob Elbert. |
Fuels from fields, forests
ISU scientists look to biorenewable resources to replace petroleum in
products
by Linda Charles
People in the United States seem to have an unquenchable thirst for
petroleum -- whether it's to power vehicles or serve as the base for myriad
products. Petroleum has changed our lives, but not always for the better.
A limited resource that mostly is imported to this country, petroleum
doesn't break down easily when made into products like plastic and it causes
environmental problems when burned.
Iowa State researchers hope to reduce our reliance on petroleum. They
believe that someday we can grow the materials for our plastics and fuels in
farm fields and forests. Numerous ISU scientists are developing ways to turn
plant and animal biorenewable resources into everything from fuel and
electricity to disposable golf tees and composite board.
Here are just a few of the uses Iowa State faculty are devising for
biorenewable resources.
Fuels from fats, oils
Tractors, trucks, buses and some cars use petroleum-based diesel fuel to
power their engines. ISU scientists are exploring an alternative --
biodiesel, which can be made from any vegetable oil or animal fat.
Today, biodiesel is mostly used as a fuel additive to lubricate the fuel
injection system. It could be used to replace diesel fuel entirely, but it's
currently too costly.
About 75 percent of the cost of biodiesel stems from the original substance
used to make the fuel. Soybean oil, which often is used, is relatively
expensive. If cheaper oils (such as used restaurant frying oil) or animal
fats (beef tallow, pork lard or chicken fat) could be used, the cost would
be dramatically reduced.
But these cheaper sources contain free fatty acids, which must be removed or
converted before the raw material can be turned into biodiesel. Standard
methods involve adding a liquid acid (the catalyst) to convert the free
fatty acids into biodiesel in the presence of methanol. However, the acid
must be removed once it has done its job, and removing a liquid from a
liquid is expensive, too.
Brent Shanks, associate professor of chemical engineering, and Victor Lin,
associate professor of chemistry, have developed a method to use a solid
substance as the catalyst. Lin bonded an acid to silica, which is much like
beach sand. As the oil flows with methanol over the silica mixture, the free
fatty acids are transformed into biodiesel (a mixture of methanol ester
derivatives of the fatty acids). The catalyst then is easily removed.
John Verkade, professor of chemistry, also is looking at solid catalysts. He
is concentrating on ways to keep different solid catalysts from dissolving
or leaching into the biodiesel. He has two promising methods. One uses an
organic compound bonded (tethered) to a silica base; the other uses an
inorganic compound that may not require tethering to another material.
Even if ISU researchers can find a more economical way to produce biodiesel,
there are other problems.
Biodiesel reduces black smoke emissions associated with petroleum-based
diesel. But in some situations, it releases more nitrogen oxide into the
air, which can contribute to smog.
Jon Van Gerpen, interim chair of the department of mechanical engineering,
is working to eliminate this problem and also improve biodiesel's
performance in cooler weather. (Biodiesel begins to gel at 32F; regular
diesel doesn't start to gel until about 15F.)
Shanks also is doing research on ethanol, a corn-based gasoline additive.
One problem in making ethanol is determining what to do with the corn hulls
that are left after the inside of the kernel is extracted. Some of the hulls
are shipped to Europe as a livestock feed additive, but Shanks said that
market is dwindling. He is working on a method to break down the hulls into
sugars, which then could be fermented into ethanol.
Bio-oil from stalks, wood
Robert Brown, director of the Center for Sustainable Environmental
Technologies, is working on a project to turn fibrous plant materials, such
as woodchips, corn stalks or oat hulls (often referred to as biomass), into
bio-oil. The product can be used as fuel in boilers, diesel engines or gas
turbines, or as a source of chemicals for the production of pesticides,
adhesives and other products.
The biomass is heated to a high temperature in an oxygen-free environment,
and the subsequent vapors are cooled into bio-oil. ISU researchers are
perfecting the process at the Biomass Energy Conversion Facility in Nevada.
Brown, the Bergles Professor of Thermal Sciences in mechanical engineering,
said the process could be ready for commercialization in a couple of years,
but noted bio-oil is more expensive than traditional sources of energy, such
as coal.
He added that Alliant Energy (which provides electric, natural gas and steam
to nearly 2 million customers) is very interested in using biomass to
generate "green" power.
Another potential fuel source under study by Iowa State researchers is
switchgrass, a native warm-season grass that once thrived in the tall grass
prairies.
E. Charles Brummer, associate professor of agronomy, is part of a team
involved in the Chariton Valley Biomass Project. The team is using
switchgrass to replace some of the coal that is burned to make electricity.
The project's goal is eventually to grow about 40,000 acres of switch-grass
to replace about 5 percent of the coal burned at the Alliant Energy's
Ottumwa Generating Station.
Tests have shown the process works. The switchgrass is harvested into bales
and sent to the generating station, where it is ground up and blown into the
furnace. Like most "green" projects involving new technology, switchgrass
will need subsidies to make it competitive with the coal industry, which
already receives many subsidies.
Switchgrass offers other environmental benefits. It helps prevent soil
erosion and and adds carbon to the soil, which promotes the growth of
beneficial bacteria.
Plastics that degrade
Jay-lin Jane and Perminus Mungara have a solution for the problem of
disposing of plastic: make it biodegradable. Professor Jane and assistant
scientist Mungara (both in the department of food science and human
nutrition) have developed plastic from animal sources (such as chicken
feathers) and plant sources (such as soybeans) that biodegrade in a month --
a good trait for products that are used once and pitched.
The team fashioned the biodegradable plastic into disposable flatware and
plates that break down when composted. Or, the plastic flatware can be
ground and reused as a soil conditioner and growth enhancer for crops.
An Illinois company uses the plastic to make golf tees. And Mungara
developed a biodegradable plastic road marker that can withstand a season's
use and be scraped off by snowplows to roadside ditches, where it degrades.
The two currently are seeking ways to shorten or extend the shelf life of
biodegradable plastics, depending on their intended uses.
Deland Myers, professor of food science and human nutrition, and other
researchers on ISU's biocomposite research team have developed a soy
protein-based adhesive technology that could be on the market in a couple of
years.
They are working with companies that hope to use it to make furniture.
The research team also developed a manure board made from -- well, the name
says it all. But composite manure board, which compares favorably with 100
percent wood composite, remains a novelty item for now. That's because no
one has figured out how to harvest, dry and store the waste economically
enough to make its production feasible.
The biocomposite research team scientists also are working on a soy
protein-based wood preservative that is safer to use and more
environmentally friendly than some of the current chemicals used to pressure
treat wood. They also are trying to make fiber-based plastic composites to
increase the rigidity of plastic (think plastic coat hangers) and reduce the
level of the petroleum-based chemicals needed.
Verkade is working on "solubalizing" (dissolving) biomass material.
Converting these materials to liquids makes it easier for enzymes to
interact with molecules, which, in turn, eases the conversion into chemicals
that eventually could be used in pharmaceuticals and organic solvents. The
Iowa Corn Promotion Board and a local co-op are interested in the process.
Verkade laughs as he admits the process he is using was discovered by
accident nearly 40 years ago by one of his graduate students. The student
complained that someone was stealing his boiling sticks. (Boiling sticks are
small wooden sticks, similar to Q-tips, used in a boiling substance to
ensure an even boil.) An investigation showed that rather than being stolen,
the substance was dissolving the wood. There was little interest in the
discovery, however, until the recent popularity of biorenewable resources.
"A lot of discoveries are made by accident," he said. "It keeps things
interesting."
|
Ames, Iowa 50011, (515) 294-4111
Published by: University Relations,
online@iastate.edu
Copyright © 1995-2003, Iowa State University. All rights reserved.
|
|